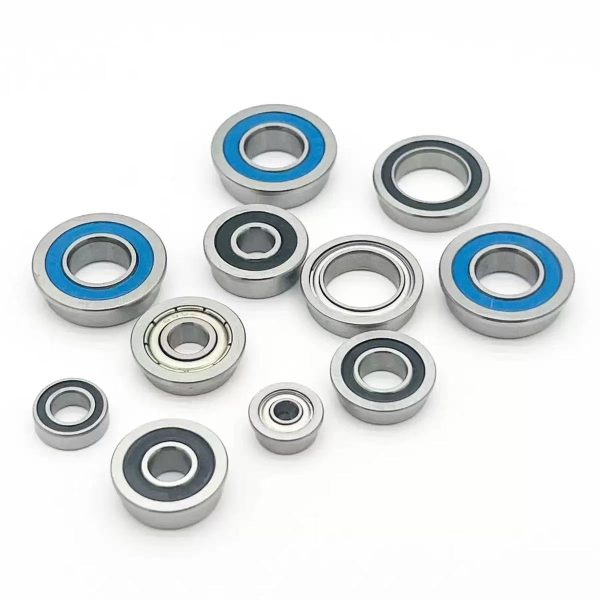
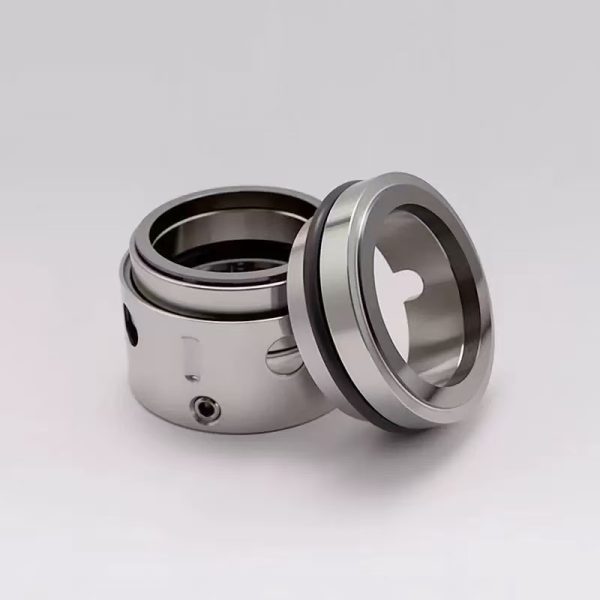
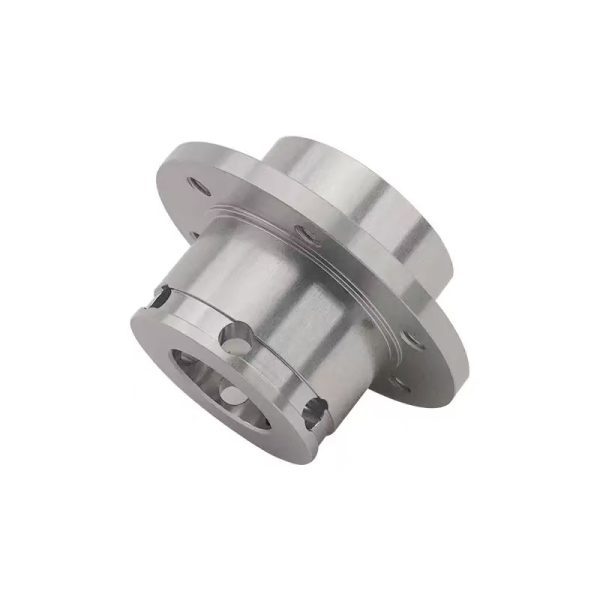
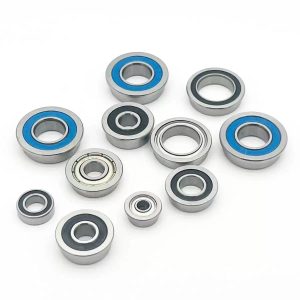
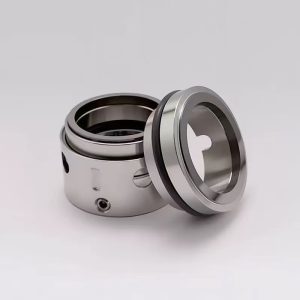
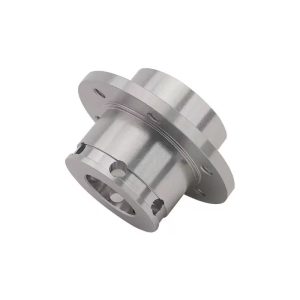
Mechanical Seals Durable CNC Turned Components for Rotary Equipment
0 out of 5
Mechanical Seals Durable CNC Turned Components for Rotary Equipment
Categoria: Small CNC Machining
Etiquetas: cnc machined fasteners, CNC Machined Parts, CNC milling parts, cnc turned parts, component mechanical seals, double mechanical seals, double mechanical seals for pumps, mechanical seals, mechanical seals in pumps, mechanical seals manufacturer, mechanical seals parts, mechanical seals pumps, mechanical shaft seals, mechanical shaft seals for pumps, metal fastener, ppc mechanical seals, pump mechanical seals, small cnc machining parts, water pump mechanical seals
- Descrição
- Avaliações (0)
Descrição
What Are Mechanical Seals?
Mechanical seals are precision-engineered devices used to prevent leakage between a rotating shaft and a stationary housing in pumps, compressors, and other fluid-handling equipment. They create a tight seal by maintaining contact between two flat, highly polished surfaces—one rotating with the shaft and the other fixed to the housing. Compared to traditional packing seals, mechanical seals offer superior performance, reduced friction, and longer service life.
Materials
Common materials used in mechanical seal include:
Primary Sealing Faces: Silicon carbide, tungsten carbide, alumina ceramic, and carbon graphite.
Secondary Seals: Nitrile rubber (NBR), fluorocarbon rubber (FKM), ethylene propylene diene monomer (EPDM), and polytetrafluoroethylene (PTFE).
Metal Components: Stainless steel (304, 316), Hastelloy, and titanium.
Surface Treatments
To enhance durability and sealing performance, mechanical seal surfaces often undergo treatments such as:
Hard Coating: Diamond-like carbon (DLC) or chromium nitride (CrN) for wear resistance.
Polishing: Ultra-fine finishing to minimize friction and leakage.
Laser Etching: Micro-texturing to improve lubrication in dry-running conditions.
Specifications
Mechanical seals vary in design and specifications, including:
Size: Shaft diameters ranging from 10 mm to over 200 mm.
Pressure Rating: From vacuum conditions up to 100 bar or higher.
Temperature Range: -50°C to +400°C, depending on materials.
Speed: Capable of handling rotational speeds exceeding 5,000 rpm.
Applications
Mechanical seals are widely used in industries such as:
Oil & Gas: Pumps in refineries and pipelines.
Chemical Processing: Handling corrosive and abrasive fluids.
Power Generation: Cooling water circulation in power plants.
Pharmaceutical: Ensuring contamination-free fluid transfer.
Water Treatment: High-efficiency pumps for desalination plants.
Excellent Case
Challenge: A chemical plant faced frequent failures in its centrifugal pumps handling highly abrasive sulfuric acid, leading to costly downtime and maintenance.
Solution: A dual mechanical seal with silicon carbide primary faces and PTFE secondary seals was installed. The seals were designed for high corrosion resistance and equipped with a flush system to prevent particle buildup.
Result: The mechanical seals achieved a service life of over 24 months—four times longer than the previous packing seals. Leakage was reduced to near zero, improving safety and operational efficiency while cutting maintenance costs by 60%.
Avaliações
Ainda não existem avaliações.