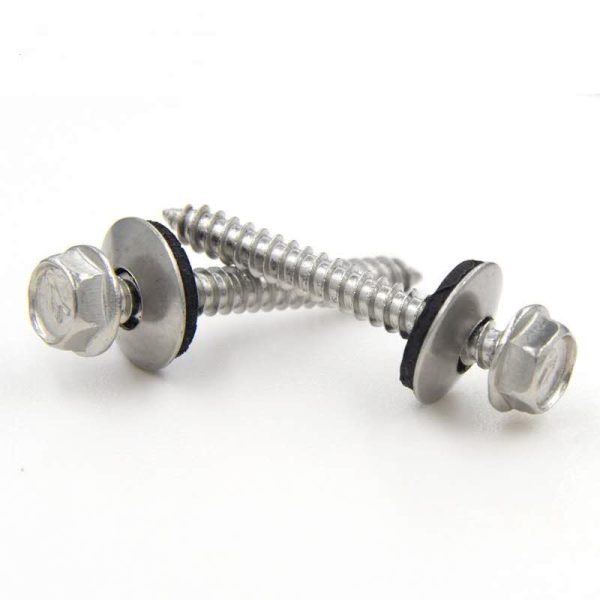
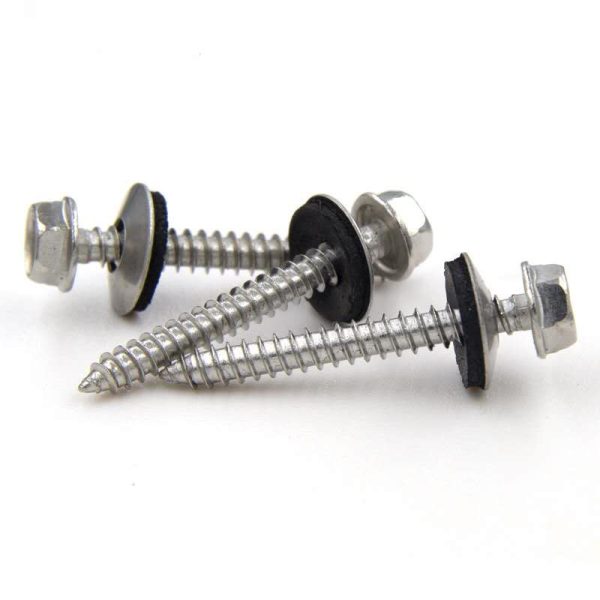
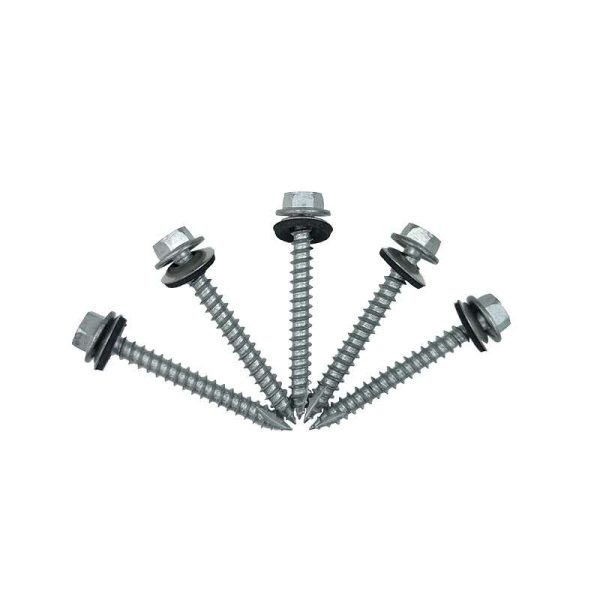
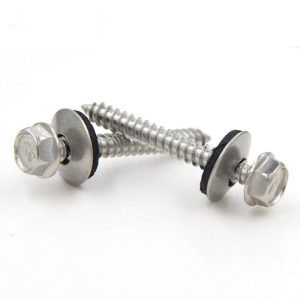
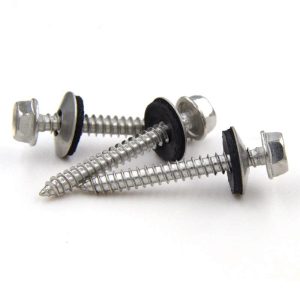
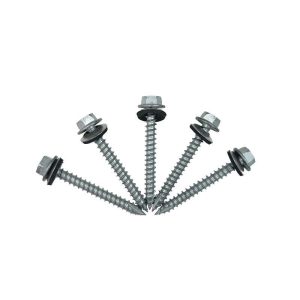
Hex Head Self Drilling Metal Roofing Screws with Washer Sheet Metal Tek Screws
0 out of 5
Hex Head Self Drilling Metal Roofing Screws with Washer Sheet Metal Tek Screws
카테고리: Machined Screws
태그: 1 inch metal roofing screws, 1 metal roofing screws, 12 metal roofing screws, 14 metal roofing screws, 2 1/2 metal roofing screws, 2 inch metal roofing screws, 3 4 metal roofing screws, 3 inch metal roofing screws, 3 metal roofing screws, cnc machined screws, cnc machining screws, installing metal roofing screws, machined screws, machining screws, metal roofing screw, metal roofing screws, metal roofing screws 2 inch, metal roofing screws for wood, metal roofing screws self tapping, metal roofing screws with rubber washer, metal roofing screws with washers, self drilling metal roofing screws, sheet metal roofing screws
- 설명
- 상품평 (0)
설명
What Are Metal Roofing Screws?
Metal roofing screws are specialized fasteners designed specifically for securing metal roofing panels to various structural surfaces. These heavy-duty screws feature unique engineering that makes them ideal for roofing applications, combining weather resistance with exceptional holding power.
Unlike standard screws, metal roofing screws include three critical components:
Self-drilling tips that penetrate metal without requiring pre-drilled holes
Sealing washers (typically EPDM rubber) that create watertight seals
Corrosion-resistant coatings that withstand decades of exposure
These metal roofing screws are the backbone of any quality metal roof installation, ensuring panels remain securely fastened while preventing leaks and resisting environmental damage.
Materials Used in Metal Roofing Screws
1. Carbon Steel
The most economical option, always coated for corrosion protection:
Hot-dip galvanized (thick zinc coating)
Electro-galvanized (thinner but more uniform coating)
2. Stainless Steel
The premium choice for harsh environments:
304 stainless: Good general corrosion resistance
316 stainless: Superior performance in coastal/salty conditions
410 stainless: Harder but less corrosion-resistant
3. Aluminum
Lightweight option for aluminum roofing systems:
Naturally corrosion-resistant
Softer than steel, requiring careful installation
Surface Finishes & Coatings
1. Zinc Coatings
Standard galvanized: 0.2 mil thickness
G90 galvanized: 0.9 mil thickness for longer life
Zinc-aluminum alloys: 5-10x more durable than plain zinc
2. Advanced Coatings
PVDF/Kynar coatings: Color-matched to roofing panels
Ceramic coatings: Extreme UV and chemical resistance
Dacromet coatings: Non-electrolytic zinc-aluminum flake coating
3. Stainless Steel Finishes
Passivated (chemically treated) surface
Bright polished or dull matte appearances
Technical Specifications
Screw Sizes
Diameter: #10 to #14 (most common is #12)
Length: 1″ to 6″ (varies by material thickness)
Threads:
Coarse for wood substrates
Fine for metal-to-metal applications
Head Styles
Hex washer head (most common)
Pan head for low-profile applications
Wafer head for standing seam roofs
Drive Types
Hex head (5/16″ most common)
Torx drive (increasingly popular)
Phillips (becoming obsolete)
Washer Types
EPDM rubber (standard)
Silicone (extreme temperatures)
Metal-backed (high wind areas)
Primary Applications
1. Residential Metal Roofing
Corrugated metal roofs
Standing seam installations
Metal shingle systems
2. Commercial & Industrial Buildings
Warehouse roofs
Factory buildings
Agricultural structures
3. Specialty Applications
Solar panel mounting
Metal wall cladding
Roof edge flashings
4. Extreme Environments
Coastal properties
Chemical plants
High-altitude installations
Premium Installation Case: Mountain Retreat Metal Roof
Project Overview
A luxury cabin in the Colorado Rockies required a roof that could withstand:
Heavy snow loads (200+ lbs/sq ft)
Temperature swings (-30°F to 100°F)
High UV exposure at 9,000 ft elevation
Material Selection
Roofing Panels: 24-gauge Galvalume standing seam
Screws: #14 x 2-1/2″ stainless steel with:
316 stainless steel construction
High-density EPDM washers
Torx drive heads
Installation Process
Substrate Preparation:
2×6 purlins at 16″ OC
Ice/water shield underlayment
Panel Installation:
Standing seam panels snapped together
Screws placed at 12″ intervals
Proper washer compression verified
Special Considerations:
Expansion joints for thermal movement
Extra screws at eaves for snow retention
UV-resistant sealant at penetrations
Performance Results
After 5 years of service:
Zero leaks despite heavy snows
No visible corrosion
Washers remain flexible
Panels show no pull-out or loosening
Why Proper Screw Selection Matters
Choosing the right metal roofing screw affects:
Longevity: Corrosion resistance determines roof life
Weatherproofing: Washer quality prevents leaks
Structural Integrity: Proper sizing prevents pull-out
Aesthetics: Color-matched screws maintain clean lines
For optimal performance:
✔ Always match screw material to environment
✔ Never mix dissimilar metals
✔ Use manufacturer-recommended lengths
✔ Replace damaged washers immediately
Conclusion
Metal roofing screws represent a perfect marriage of engineering and material science. When selected and installed correctly, they create roofing systems that last 50+ years with minimal maintenance. Whether you’re building a simple shed or a high-end commercial facility, investing in quality screws ensures your metal roof performs as intended for decades to come.
상품평
아직 상품평이 없습니다.