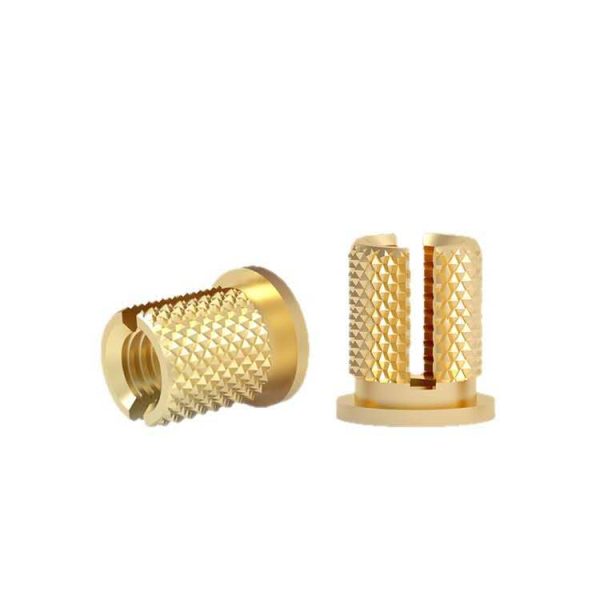
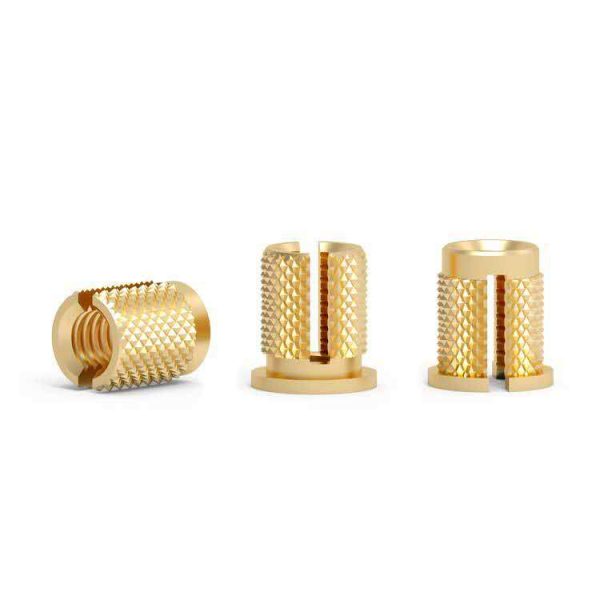
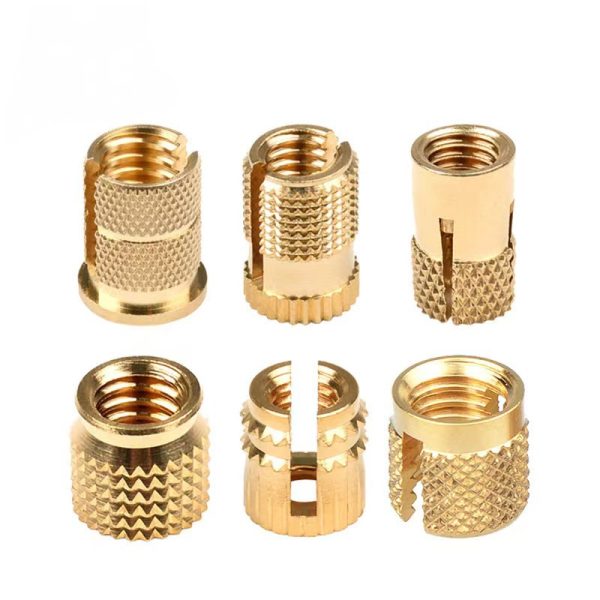
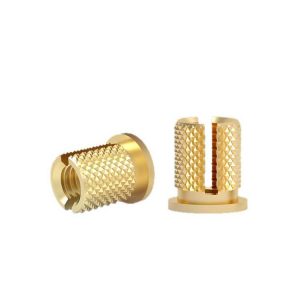
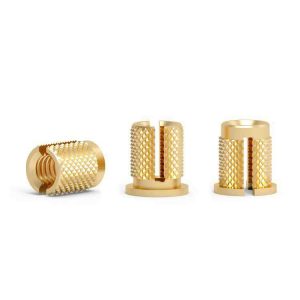
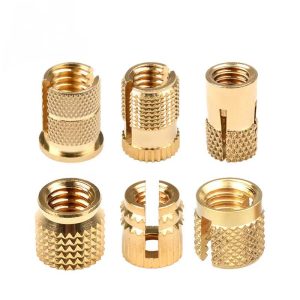
Slotted Brass Press in Threaded Insert Knurled Press Fit Threaded Inserts
0 Sur 5
Slotted Brass Press in Threaded Insert Knurled Press Fit Threaded Inserts
Catégorie : Inserts filetés
Étiquettes : 1 4 20 threaded insert, 1/2 threaded inserts, 1/4 in threaded insert, 3 8 threaded insert, 5/16 threaded inserts, brass knurled insert, brass knurled inserts, brass threaded insert, Brass Threaded Inserts, knurled insert, knurled inserts, m3 threaded insert, m5 threaded inserts, m8 threaded insert, press fit threaded insert, press fit threaded inserts, press in threaded insert, press in threaded inserts, threaded insert, threaded insert 1 4 20, threaded insert 1/4, threaded insert 3/8, threaded insert 5/16, threaded insert m3, threaded insert m4, threaded insert metal, threaded inserts
- Description
- Avis (0)
Description
What is a Press In Threaded Insert?
A press in threaded insert is a precision fastener designed to create durable, reusable threads in softer materials that would otherwise strip or wear out. These inserts are mechanically pressed or hammered into a pre-drilled hole, providing a reinforced threaded surface that withstands repeated assembly and disassembly. Unlike self-tapping screws that cut their own threads, press-in inserts preserve material integrity while offering superior load distribution.
Materials Used for Press In Threaded Inserts
Press in threaded inserts must balance strength with installation characteristics. Common materials include:
Carbon Steel – The most economical choice for general-purpose applications with moderate stress requirements.
Stainless Steel (304/316) – Offers excellent corrosion resistance for marine, medical, and food-grade applications.
Brass – Ideal for electrical components and plumbing where corrosion resistance and non-sparking properties are critical.
Aluminum – Used in aerospace and automotive applications where weight reduction is paramount.
High-Strength Alloys (Inconel, Titanium) – Reserved for extreme environments like jet engines or chemical processing equipment.
Surface Treatments for Enhanced Performance
Specialized coatings and treatments extend insert lifespan and functionality:
Zinc Plating (Yellow/Black) – Basic corrosion protection for indoor steel inserts.
Electroless Nickel – Superior wear resistance with consistent coating thickness in complex geometries.
PTFE (Teflon) Coating – Reduces friction during installation while providing chemical resistance.
Passivation (Stainless Steel) – Removes free iron particles to maximize corrosion resistance.
Anodizing (Aluminum Inserts) – Hardens surface while allowing color-coding for different thread sizes.
Critical Specifications
Press in threaded inserts are defined by precise dimensional characteristics:
Insert Diameter – Ranges from M2 (2mm) to M24 (24mm) in metric sizes, with corresponding imperial equivalents.
Grip Length – Typically 1.5x to 3x the thread diameter for optimal holding power.
Knurl Pattern – Diamond, straight, or helical knurling to prevent rotation after installation.
Drive Style – Hex, slotted, or external wrench flats for installation tool compatibility.
Temperature Rating – Standard inserts handle -40°C to 120°C; high-temp variants exceed 500°C.
Industry Applications
These versatile fasteners solve threading challenges across industries:
Automobile – Door hinge reinforcements and engine component mounts in aluminum blocks.
Aerospace – Secure avionics mounting in composite airframe structures.
Medical Devices – Sterilizable threads in imaging equipment and surgical tools.
Consumer Electronics – Durable threads in plastic laptop housings and VR headsets.
Industrial Machinery – Wear-resistant threads in polymer conveyor components.
Excellent Case: Reinforcing Carbon Fiber Drone Frames
A leading drone manufacturer faced chronic thread stripping in their premium carbon fiber racing frames. The lightweight material couldn’t withstand repeated battery and camera changes, leading to costly warranty claims.
Innovative Solution
The engineering team implemented stainless steel press in threaded inserts with:
Helical knurling for maximum pull-out resistance
Electroless nickel coating to prevent galvanic corrosion
M3 thread size matching existing components
Measurable Results
✔ 87% reduction in stripped thread incidents
✔ 30% faster battery swaps during races
✔ 5-year lifespan projection vs. original 6-month failure rate
✔ Weight-neutral solution maintaining critical balance
The inserts became standard across their product line, transforming a reliability weakness into a competitive advantage.
Installation Best Practices
To maximize performance:
Precision Drilling – Hole diameter must match insert specs within ±0.05mm
Proper Tool Selection – Use arbor presses or calibrated hand tools
Alignment Verification – Confirm perpendicularity before pressing
Post-Installation Inspection – Check thread engagement with gauge pins
Conclusion
Press in threaded inserts represent engineering elegance – simple in concept but transformative in application. They bridge the gap between material limitations and mechanical requirements, enabling lighter, stronger, and more maintainable designs. Whether you’re working with delicate composites or high-volume plastics, these inserts deliver thread reliability that outlasts the parent material.
For mission-critical applications, always specify military-spec (MS) or ISO-certified inserts from qualified suppliers to ensure consistent performance under stress. The right insert doesn’t just solve a fastening problem – it future-proofs your design.
Avis
Il n’y a pas encore d’avis.